|
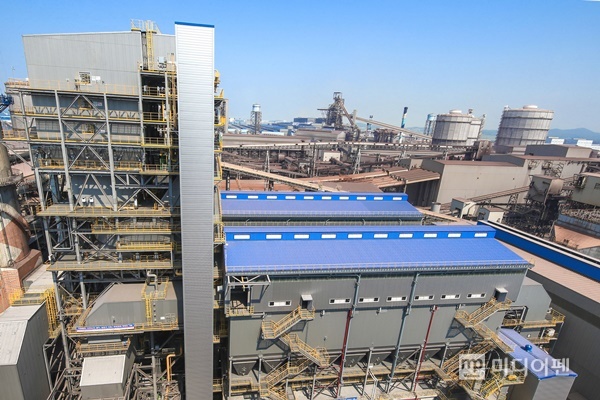 |
|
▲ 당진제철소 소결 배가스 설비 전경. /사진=현대제철 제공 |
[당진/미디어펜=권가림 기자] ‘자동차소재 전문 제철소’·‘세계 최고의 제품 포트폴리오 갖춘 제철소’·‘최첨단 시설’. 현대제철 당진제철소를 가리키는 수식어는 여럿 있지만 지난 9일 찾은 당진제철소는 그 무엇보다 '친환경제철소'란 말이 잘 어울리는 곳이었다.
서울 광화문에서 자동차로 1시간 30여분을 달려 충청남도 당진에 있는 현대제철 당진제철소에 도착했다. 공장 내부에 진입하는 차량은 깐깐한 검문을 받고 있었다. 제철소 보안을 위해 기자 역시 휴대폰 앞뒤 카메라에 보안 스티커를 붙여야 했다.
서울 여의도 3배(882만㎡)에 달하는 제철소 곳곳을 버스를 타고 둘러봤다. 지구 반대편에서 원료를 싣고 온 대형 선박들과 하역 설비 모습만으로도 부두의 웅장함을 느끼기에 충분했다.
당진제철소는 철의 원료인 철광석을 브라질과 호주에서 배로 연 2300만톤을 수입한다.
수입 철광석과 유연탄 등은 하역 후 터널형 컨베이어 벨트로 떨어진다. 이 원료들은 현대제철이 세계 최초로 도입한 밀폐형 원료 저장고로 또 다시 옮겨진다. 높이 60m, 지름 120m에 달하는 둥근 ‘돔’ 형태의 거대한 원료 저장시설로 들어서니 구슬 모양의 철광석과 가루 철광석이 양쪽으로 나뉘어 돔 벽쪽에 산처럼 쌓여있었다. 이렇게 쌓인 철광석들은 철광석을 긁어 아래로 떨어뜨리는 장비인 블레이드에 의해 지하에 설치된 컨베이어벨트로 이동된다.
송기원 당진제철소 홍보팀 과장은 “이 돔 안에 32만톤의 철광석을 쌓아 올릴 수 있다”며 “기후조건에 영향을 받지 않을 뿐만 아니라 적치 효율성도 향상됐다”고 설명했다.
철광석 중 흙가루 형태의 철광석이 80%인데 고로(용광로)에 넣기 전 ‘소결과정’을 거쳐 덩어리로 만든다.
친환경제철소로 거듭나기 위한 현대제철의 노력은 이 소결공정에서 확인할 수 있었다.
철광석을 정제하는 소결공정에서는 황산화물, 질소산화물 등 제철소 대기오염물질의 90% 이상을 배출한다. 기존 저감장치는 숯을 활용해 먼지를 제거했지만 잦은 장치 고장, 화재 등이 발생하자 현대제철은 소결로 SGTS에 약 4100억원 규모의 투자를 결정했다. SGTS는 소결과정에서 발생하는 질소산화물 등을 촉매와 중탄산나트륨을 통해 제거하는 친환경 시설이다.
|
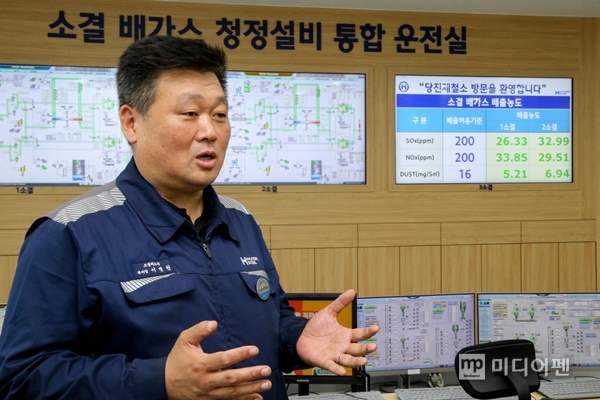 |
|
▲ 현대제철 당진제철소 관계자가 소결배가스 청정설비에 대해 설명하고 있다. /사진=현대제철 제공 |
SGTS의 저력은 환경상황실에서 검증할 수 있었다.
오른쪽에 자리 잡은 모니터에는 지난 5월 28일과 6월 13일 정상 가동을 시작한 1·2소결공장의 황산화물, 질소산화물, 먼지 배출 현황이 나타났다. 이날 현대제철 제1소결공장의 황산화물 배출량은 26.33ppm, 제2소결공장은 32.99ppm으로 규제당국의 1일 배출허용기준인 200ppm을 크게 밑돌았다. 먼지도 기준치 16mg보다 낮은 5.21mg, 6.94mg를 나타냈다.
소결로 굴뚝 아래에 설치된 측정소에서 실시간으로 전송된 해당 데이터는 한국환경공단 중부권 관제센터와 환경부, 충남도, 당진시 등에도 공유된다.
이승희 당진제철소 홍보팀장은 “충남도 조례기준이 오는 2020년 강화된다”며 “황산화물의 1일 배출허용기준은 84ppm, 질소산화물은 105ppm로 변경되지만 현재 배출농도는 이 기준의 40% 수준”이라고 강조했다.
“오래되지 않은 설비를 뜯어내고 4000억원을 투자하는 것은 어려운 결정이었다. 내년 6월 SGTS 3기까지 모두 완공되면 당진제철소의 연간 대기오염물질 배출량은 절반으로 줄을 것”이라고 말하는 안동일 현대제철 사장의 눈에도 자신감이 보였다.
|
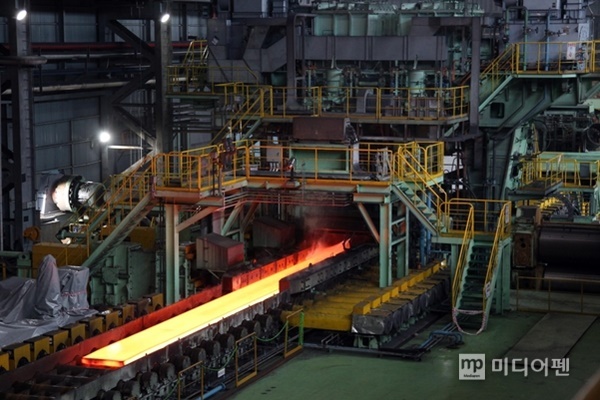 |
|
▲ 빨갛게 달아오른 슬라브가 오른쪽에서부터 회전하는 롤 위를 지나가며 1200도의 열과 6000톤의 압연 하중을 거치고 있다. /사진=현대제철 제공
|
안전모와 마스크를 착용한 채 당진제철소 제2열연공장으로 발걸음을 옮겼다. 들어서자마자 연신 쿵쾅거리는 소음이 귓가에 울렸다. 3~4층 높이에서 공정을 내려다보는데도 화끈한 열기가 얼굴에 훅 끼쳐오며 이마에 땀이 송글송글 맺혔다. ‘철’ 냄새가 진동할 것 같았지만 예상은 빗나갔다.
약 10m 길이, 25cm 두께의 빨갛게 달아오른 슬라브(널빤지 모양의 철강 반제품)가 오른쪽에서부터 회전하는 롤 위를 지나갔다. 슬라브는 제강 공정을 거친 쇳물이 비로소 특정한 형태를 띠는 첫 단계 제품이다. 1250도의 열과 6000톤의 압연 하중으로 이 슬라브는 길이가 약 1000m로 늘어나고 두께는 최대 1.2mm로 얇아진다. 공정이 끝나면 냉연공장에서 산세, 압연, 급랭, 도금을 거쳐 최종제품(냉연강판)으로 탄생한다. 제2열연공장의 생산능력은 연간 550만톤으로 자동차 강판, 건축물 외장재, 송유관 등으로 사용된다.
안 사장은 “부임한 지 4개월여 만에 각종 환경문제가 발생해 죄송할 따름”이라며 “지역 시민단체, 주민, 기관 지차제 등과 소통을 강화하고 환경개선을 위한 적용 가능한 기술을 모색해 친환경제철소로 성장할 것”이라고 밝혔다.
이어 “안전이 문화로 자리 잡을 수 있도록 노력하고 글로벌 수출 경쟁력도 키워나갈 방침”이라고 덧붙였다.
[미디어펜=권가림 기자]
▶다른기사보기