[미디어펜=홍샛별 기자]“이곳에서는 트윈워시에서부터 건조기, 스타일러, 통돌이 세탁기까지 다양한 의류 관리 가전 제품이 11초에 1대 꼴로 생산되고 있습니다.”
|
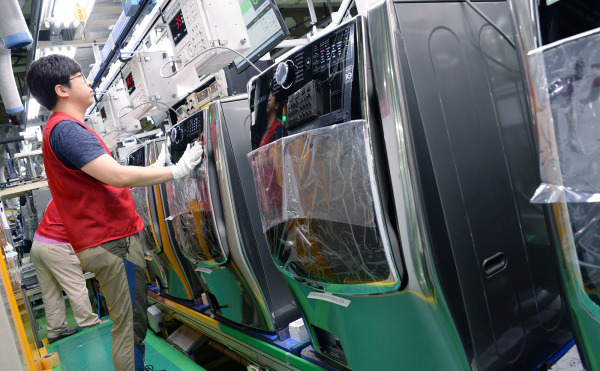 |
|
▲ LG전자 직원이 지난달 31일 창원2공장에서 제조된 드럼세탁기를 검사하고 있다. /사진=LG전자 제공 |
지난달 31일 의류 관리 가전의 메카로 불리는 LG전자의 ‘창원 2공장‘. 박인섭 LG전자 리빙어플라이언스 제조팀장은 제품 생산으로 분주한 A1동 제조 라인을 둘러보며 이처럼 설명했다.
길이 약 140m 정도의 제조 라인에서는 세탁기, 건조기 등 의류 관리 가전 제품이 쉴 새 없이 만들어지고 있었다. 특히 생산 효율화를 위한 자동화 설비가 눈길을 끌었다. 현재 의류 관리 가전의 제조라인 자동화율은 60%에 달한다.
천장에 설치된 약 20m 길이의 트롤리(Trolley)는 무겁고 부피가 큰 세탁조를 쉴 새 없이 제조 라인으로 보내 주고, 부품 자동 공급 설비(SPS)는 도어·상판 등 제품 조립에 필요한 부품을 작업자의 손이 닿을 정도의 가까운 거리까지 옮겨 줬다.
박 팀장은 “제품을 만들기 위한 대형, 중형, 소형 부품이 각각 30분, 2시간, 4시간 주기로 공장에 들어온다”며 “하루에 공장에 들어오는 부품의 양만 해도 5t 트럭 950대 정도 된다”고 자동화 설비의 필요성을 설명했다.
여러 단계의 조립 과정을 거쳐 완성된 제품은 곧바로 품질 검사에 들어갔다. 세탁기의 품질 검사를 곁에서 지켜본 결과 작업자가 세탁통 내부에 물을 채워 헹굼, 탈수 등 기능의 정상적 작동 여부를 꼼꼼히 점검하는 걸 확인할 수 있었다.
이처럼 까다로운 품질 검사를 통과한 제품만이 제조 라인 마지막 단계인 포장 공정에 이를 수 있다. 포장은 자동화 설비가 맡는다. 자동 점검 시스템은 포장 박스 내 액세서리와 부품까지도 확인한다.
포장 공정을 마친 제품들이 모여 있는 공간은 공장의 규모와는 달리 협소했다. 공장의 한 관계자는 ‘무창고 시스템’을 운영하기 때문이라고 설명했다.
|
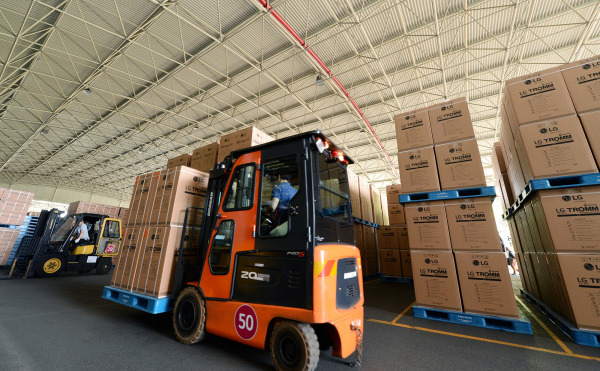 |
|
▲ LG전자 직원들이 지난31일 창원2공장에서 생산된 LG 드럼세탁기 제품들을 부지런히 실어나르고 있다. /사진=LG전자 제공 |
실제 창원 공장의 제조 라인 끝에는 컨테이너 32개가 대기하고 있다. 완성된 제품은 즉시 각각의 컨테이너에 실려 이송된다. 국내 판매 물량의 경우 전국의 물류 창고로, 수출용 제품의 경우 약 40분 거리에 있는 부산항으로 옮겨지는 것이다.
제조 라인에 이어 방문한 곳은 제품 성능을 책임지는 ‘신뢰성 시험동’이었다.
신뢰성 시험동에서는 고온, 저온 등의 환경에서 이뤄지는 ‘온도 시험’부터 제푸의 문을 1만회 이상 반복적으로 여닫는 ‘도어 개폐 시험‘, 세탁통을 1분에 1000번까지 회전시키는 ’과진동 시험‘ 등이 이뤄진다.
특히 온도 시험의 경우 8개의 시험실의 온도와 습도를 각각 달리해 다양한 환경에서의 내구성 등을 테스트한다. 고온 시험의 경우 내부 온도가 70~80℃에 달하는 방에서 진행되며, 저온 시험은 영하 10℃ 정도에서 이뤄진다. 부품의 경우에는 영하 40℃의 극한 환경에서의 테스트도 반복한다.
혹독할 정도의 신뢰성 시험을 거치는 이유는 단 하나다. 소비자들이 만족할 수 있는 품질의 제품을 선보이기 위해서다.
이 같은 노력 덕분인지 LG전자의 세탁기는 최근 미국 소비자 신뢰도 평가에서 전자동 및 드럼 세탁기 부문의 1위를 차지하기도 했다.
김철융 LG전자 의류 관리 가전 생산 담당 상무는 "생산 라인의 효율성을 높이는 동시에 세계 최고의 품질을 위한 신뢰성 시험을 지속 강화해 의류 관리 가전에서 LG를 1등 브랜드로 만들 것"이라고 강조했다.
[미디어펜=홍샛별 기자]
▶다른기사보기