[미디어펜=박규빈 기자]"우리 진천 공장의 면적은 축구장 26개와 같아 세계 최대 규모이며, 미국·일본·독일 태양광 모듈 시장 점유율 1위를 기록하고 있습니다."
|
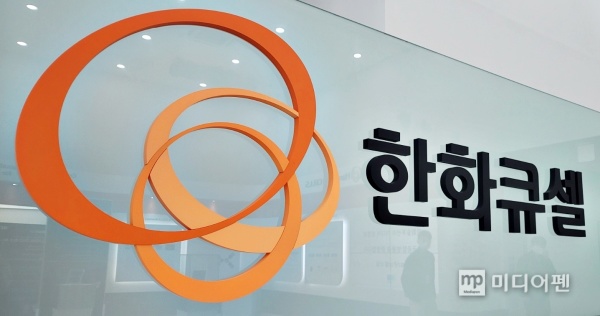 |
|
▲ 한화큐셀 로고./사진=미디어펜 박규빈 기자 |
지난 12일 기자는 충청북도 진천군 산수산업단지 소재 한화솔루션 큐셀 부문(한화큐셀) 공장에 다녀왔다.
연 면적 19만380제곱미터(약 5만7000평), 진천 1·2동으로 이뤄진 이곳에서는 지난해 말 기준 720만 명이 1년 간 사용할 수 있는 4.5기가 와트(GW)분의 태양광 셀과 1.6GW의 모듈을 각각 12개, 8개 라인에서 생산하고 있었다. 지난해 말 기준 이곳의 주요 생산 제품은 156개의 셀을 탑재한 'Q.PEAK DUO XL 9.3·10.3 시리즈로, 발전 효율은 20.9~21.6%다.
우선 공장 내 출입 전, 오염을 막기 위해 일회용 부직포 머리망을 쓰고 덧신을 신었다.
엘리베이터를 타고 3층에 들어서니 태양광 셀의 소재인 웨이퍼 입고부터 모듈 출하까지 총 7종의 공정이 자동화 과정으로 진행되는 스마트 팩토리가 펼쳐졌다.
|
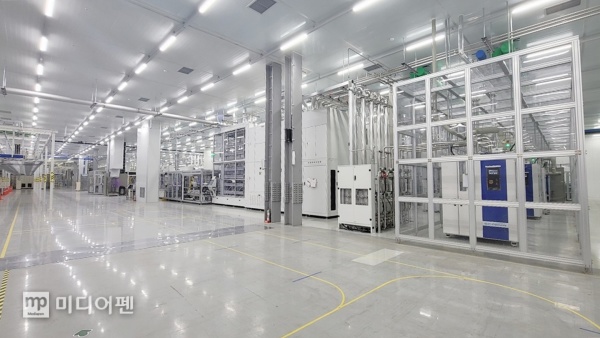 |
|
▲ 한화큐셀 진천 2공장 셀 생산 라인 내부 전경./사진=미디어펜 박규빈 기자 |
인솔자였던 이용우 한화큐셀 프로는 "진천 2공장 셀 생산 라인은 330m 가량 되고, 장비 2대가 1개 라인을 구성한다"며 "가장 먼저 웨이퍼 인스펙션(인스)는 실리콘 기반의 웨이퍼가 셀을 만들 때 적합한 물품인지 확인해주는 문지기 역할을 한다"고 말했다.
이곳에서 감지된 불량품에 대해서는 공정 담당자가 동일한 무게의 웨이퍼로 치환을 해온다는 설명도 이어졌다.
한화큐셀 진천 공장에서는 일 평균 200만 장 규모의 셀이 만들어진다. 현장에는 '트라큐(Tra-Q)' 시스템을 구축해뒀다. 이는 생산된 제품 전면에 제조 라인·일자·자재 정보를 수집해 공정을 최적화하는 데 활용하는 식별 기호를 레이저로 새겨 품질 데이터를 관리해 불량률을 낮춰주는 역할을 한다.
이와 관련, 웨이퍼가 어느 공정을 통해 셀로 가게 됐는지를 빅 데이터로 축적했고, 웨이퍼 외관에 칩이나 크랙과 같은 에러도 잡아낸다는 게 이 프로의 전언이다.
공장 부지가 굉장히 넓었음에도 불구하고 근무자는 10명이 채 되지 않아보였다. 이곳에서는 △공장 내 물류 이동 △작업 환경 제어 △불량 관리 현황 등이 실시간으로 모니터링 되고 있어 인력 소요가 크지 않았다. 머리 위에는 오토매틱 머터리얼 핸들링 시스템(AMHS)이 가동돼 생산품들이 정해진 경로에 따라 이동하고 있었다.
이 프로는 두 번째 공정인 '알칼라인 텍스처링'을 보여줬다. 그는 "웨이퍼 표면 중 거울처럼 반짝거리던 부분을 '피라미드'라고 부르는데, 화학 약품으로 요철을 형성하는 에칭 과정을 통해 빛을 효과적으로 흡수할 수 있게 만든다"고 말했다.
|
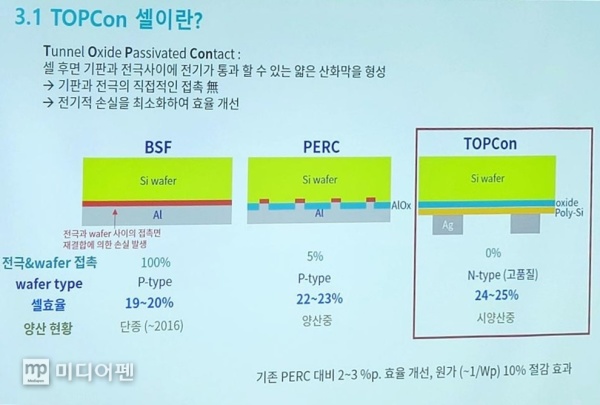 |
|
▲ 탑콘 셀 개념 설명./사진=미디어펜 박규빈 기자 |
한화큐셀은 지난 5월 총 1800억 원을 투자해 국내 공장의 셀 생산 능력을 기존 연간 4.5GW에서 5.4GW로 확대하는 계획도 발표한 바 있다. 이 중 1300억 원은 내년까지 탑콘 셀 양산을 위한 라인 전환과 설비 도입에 쓰인다. 이에 따라 내년 4월부터는 연간 3.9GW의 퍼크 셀과 1.5GW의 탑콘 셀을 생산할 수 있게 된다.
최경덕 한화큐셀 운영팀장은 "탑콘 셀 제조 공정은 기존 퍼크 셀 제조공정과 호환성이 높다"며 "이미 대규모 퍼크(PERC) 셀 제조 라인을 보유한 진천 공장에서 제조하기에 적합하다”고 언급했다.
이 프로는 셀 생산 라인 투어 중 '900℃'를 강조했다. 실리콘은 1600℃에서 용융(熔融)돼 액체 상태로 존재하는데, 900℃는 표면 반응을 시작할 수 있게 해주는 경계 조건이다. 그는 이 온도에서는 '보론'이라는 물질을 주입해 표면에 토핑을 한다는 말도 곁들였다.
여기까지가 P형 웨이퍼에 N층을 깔아 전자가 P극과 N극을 오가며 전력을 생산할 수 있도록 하는 'N층 확산 공정'이었다. 그 이후 공정들은 분리된 전자와 전공을 어떻게 효율적으로 빼낼지, 고효율을 이뤄내는 지에 초점이 맞춰져 있었다.
터널링 옥사이드(TO, Tunneling Oxide)는 전기가 통하지 않게 만드는 부도체로, 양자역학에 나오는 개념이다.
이 프로는 "호핑 커런트 내지는 터널링 커런트라고 하는데, 이것이 형성돼 셀 구조에 적용하고 있다고 보면 된다"고 전했다.
유리와 석경의 화학적 구조는 같지만 전자의 경우 오래 쓰면 아래쪽이 두꺼워지고 위쪽이 얇아진다. 때문에 업계에서는 유리를 아주 느린 형태의 액체라고 보고 있다. 이 부분에 900℃ 가량의 열처리를 통해 결정성을 가진 물질로 바꿔주는 게 이 과정의 역할이다.
다음 공정에서는 후면 보호막을 증착해 요철 구조로 형성했던 면에 층을 쌓고, 하늘색의 표면을 갖추게 되는 모습을 보게 됐다. 이는 플라즈마를 통해 얇게 필름처럼 도포하는 것으로, 전기가 통하지 않게 해주고 보온 안정성을 가진 보석 '사파이어'의 화학적 구성과 동일하다고 이 프로는 전했다.
이 단계에서 아직 반대쪽 면의 경우 아직 짙은 회색인 상태로 남아있는데, 마찬가지로 코팅 작업으로 전기적 특성을 지니게 함으로써 '전장 공정'은 끝나게 된다.
이후 셀에서 생성된 전기의 이동 통로를 만드는 '전극 형성'을 레이저를 통해 하게 되는데, 미세한 나머지 눈으로 확인할 수는 없었다. 이후에는 부착된 전기에 치약과 같은 액체-고체 사이의 물질을 말라 전류가 흐르도록 했다. 그러나 이 자체로는 전기가 통하게 할 수 없는데, 이물질이 많아 이를 태워주는 열처리 과정이 필요하다는 설명이다.
셀 공정의 마지막 순서는 다음 공정으로 보내 모듈로 제작이 되도록 하는 '소터 앤 패스터'라는 것이다. 안정적인 모듈 출력을 위해서는 비슷한 등급의 셀들이 모여야 효과적이다. 평균값을 벗어나는 제품이 껴있을 경우 해당 부분에서 전기가 통하는데 장애물로 작용하기 때문이다. 계측 결과는 디스플레이에 표시된다.
|
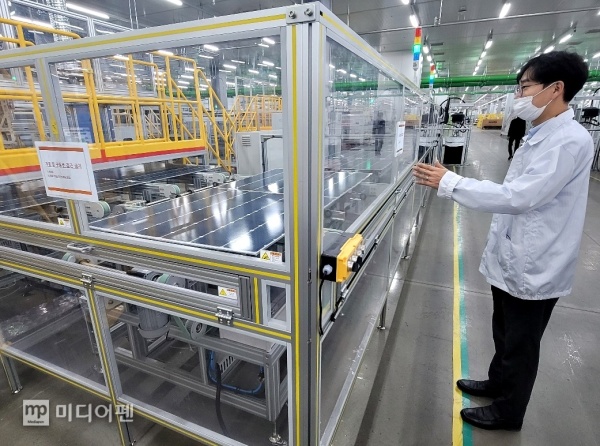 |
|
▲ 한화큐셀 관계자가 생산 현장을 둘러보고 있다./사진=미디어펜 박규빈 기자 |
이후 1층 모듈 공정으로 가보니 더욱 분주한 모습이 연출됐다.
현장 관계자는 "셀 공정에서 나온 완판 풀셀을 반으로 잘라 와이어로 연결·배치해 셀 매트릭스를 이룬다"며 "하프 셀로는 156개, 풀 셀로는 78개가 들어간다"고 답변했다.
규격 표준화 여부에 대해 그는 "다른 회사 제품과 길이는 1~2mm 가량 날 수 있지만 업계 표준은 156개"라며 "생산된 셀에서 몇 와트 짜리가 나오는지가 가장 중요하다"고 부연했다.
|
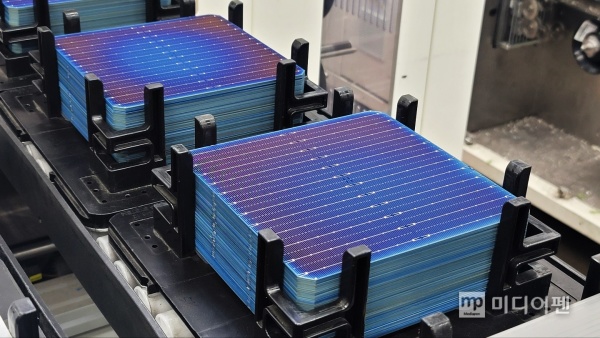 |
|
▲ 모듈화 작업을 거친 태양광 셀./사진=미디어펜 박규빈 기자 |
이후 전면 유리·EVA·셀 매트릭스·EVA·후면 유리·백시트 로딩과 각 자재를 압착하여 하나로 합치는 라미네이팅을 거치면 25~30년 간의 보존 신뢰성을 갖게 된다는 이야기도 나왔다. 한화큐셀 측은 라미네이팅을 하고 나면 빠져나온 EVA·백시트를 깎아내고, 모듈 안정성을 높이기 위해 실리콘 등을 단단하게 굳히는 큐어링을 한다.
마지막으로 제곱미터 당 1000W의 빛을 비춰 전기가 얼마나 생성되는지, 또 성능과 모듈 내에 결함이 있는 지를 확인하는 EL 테스트를 마치는 장면을 볼 수 있었다.
[미디어펜=박규빈 기자]
▶다른기사보기